Extraction system video – brief and to the point
Benefits of the eurolaser extraction systems:
- Always maximum cut quality everywhere on the table
- Individual table concepts for different materials, can also be combined
- Faster, securer extraction while cutting acrylics due to small openings in our raster plate
- Upward and downward extraction can be controlled separately
- Even suction pressure everywhere on the table
- Best ambient air in the vicinity of production
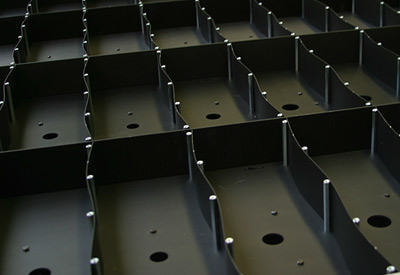
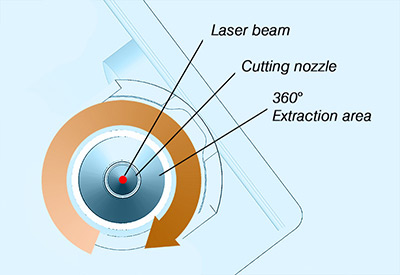
All eurolaser laser cutting systems are equipped with well-conceived 360° extraction systems.
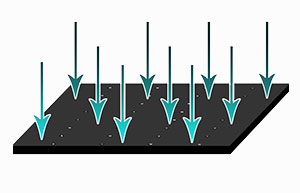
How is the high cutting quality ensured over the entire work area?
An even, full-surface distribution of the exhaust performance over the entire work area is achieved for example by means of up to 6,400 exhaust points or a full-surface honeycomb structure with a thin web over the entire surface of the table. As exhaustion has a decisive impact on the cut edge, we guarantee you a consistently high cut quality everywhere on the table.
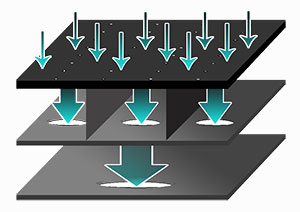
How do we achieve this powerful extraction performance?
Once the cutting emissions have been evacuated underneath the material, they are concentrated at individual exhaust segments. This creates a strong vacuum that is the basis of the exhaust performance. Subsequent concentration at a few outlets enhances this effect even further. You get optimum extraction directly at the cutting gap.
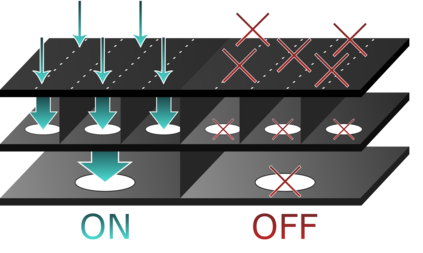
How do we achieve this powerful extraction performance?
Once the cutting emissions have been evacuated underneath the material, they are concentrated at individual exhaust segments. This creates a strong vacuum that is the basis of the exhaust performance. Subsequent concentration at a few outlets enhances this effect even further. You get optimum extraction directly at the cutting gap.
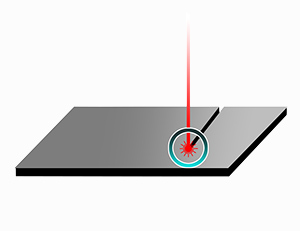
Why is the extraction concept from eurolaser better than standard extraction systems?
With our extraction concept, you get optimum performance exactly where it is needed – directly at the cutting gap. The individual segments concentrate the suction performance on a relatively small area. This minimises the loss of power due to air leak, so the power output remains consistent. In other extraction concepts, extraction of the entire work area is often effected via one large V-shaped substructure with one turbine outlet. So, the exhaust capacity is distributed and therefore, not consistently strong everywhere. In the case of long cutting gaps, this setup has a lot of air leak that over time reduces the actual exhaust performance at the cutting gap. The result is uneven cut edges and a heightened build-up of smoke deposits. As a rule, several small exhaust turbines are used at eurolaser, which always supply the individual areas of the table with the full performance capacity.
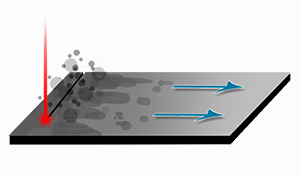
What is the advantage compared to lateral extraction?
In the case of closed table systems, ambient air is often evacuated via lateral exhaust slots that are normally located at the rear. This air flow then draws the smoke particles and soiling right across the entire material. eurolaser prevents this undesired side effect by using an additional upper exhaust unit.
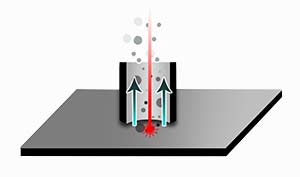
Why do we use an additional upper extraction unit?
The upper extraction unit ensures extraction of the cutting emissions that arise. This system is of particular importance for operations in which the function of the lower extraction unit is restricted. Typical examples here include engravings or kiss cuts, where the material is not completely cut through. In this case, the emissions that arise above the material cannot be extracted from below through a cutting gap. The upper exhaust unit sucks the air around the laser beam directly upwards, evenly and in a circular movement.
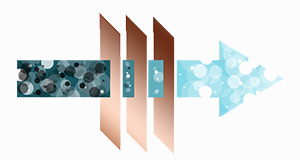
Is it possible to filter the emissions?
We offer different filter concepts for filtering coarse, fine and gaseous substances depending on your requirements. Our range even includes industrial solutions that are also suitable for plants with ecological certification.
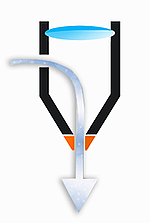
What impact does the incoming compressed air have on the cut quality?
The targeted air flow forces the material melts out of the cutting gap and cools the heat-affected zone. The stream of compressed air is vacuumed off downwards through the cutting gap. In addition the overpressure protects the optical lens against soiling. The compressed air has a significant impact on the laser cutting.
Do you have any questions? We are pleased to advise you.