Processes, material and fields of application of back-molded foils:
As an aid to better understanding of the process, we will give you here a very simplified explanation of foil back-molding. First of all, a foil material is selected which, due to its material properties, is best suited for the conditions of use it will subsequently be subjected to. The next step is to carry out the printing, which is decisive for visual appearance later on. The foils are then cut to size in the mold and injected from the back (injection molding). The results are plastic parts that ideally match their intended purpose. In the automotive sector such parts include center consoles, speedometer dials, trimming, emblems and displays etc. The reason why this process is so wide spread is simple.
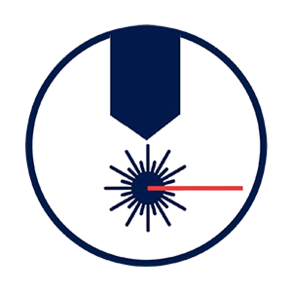
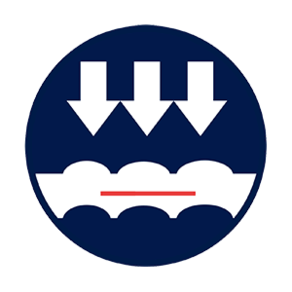
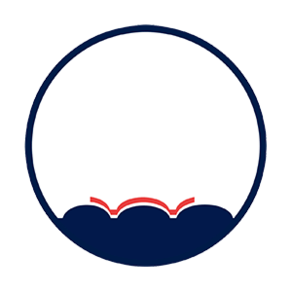
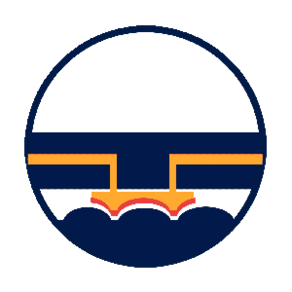
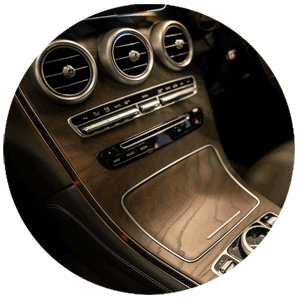
The plastic parts produced in this way can be manufactured relatively quickly, flexibly and cheaply and thanks to the print can be made in any décor whatsoever. If you look into the cockpits of today’s cars you will see trimming and center consoles in deceptively real-looking wood or carbon décor. These are all back-molded foils. They come in many different designs, depending on what the customer wants in high-gloss, carbon, chrome or metal finishes, in a structured look, with brushed metal or wood decors and in many different colors. The fields of application are as diverse as the myriad of designs themselves. The most commonly used foils are ones made of polycarbonate, polypropylene, acrylate, PET-G or polyester.

Processing of back-molded foils:
The foils are cut with die cutters, laser or knife plotters depending on the production volume and accuracy of detail required. The cutters score through high speed, which makes them very cost-effective for medium and large series. However, the expensive production of the cutting die pushes costs up and makes production unprofitable for small series. Where printed foils are concerned, which must be cut out so accurately that they subsequently fit into bordering areas perfectly, the die is often not accurate enough.
Knives get blunt over time causing a loss in cutting quality. Follow-up costs for tool replacement and the machine downtimes this involves are inevitable.

Laser cutting scores points where accuracy is concerned. Back-molded foils are very often printed and this makes the use of a camera necessary during processing. The material is positioned using reference marks. This ensures exact cutting along the printed contour. The material does not have to be fixed because laser cutting is a contact-free process. The contour can be adapted flexibly without any great effort. So even small series or one-off products can be cut profitably.
Do you have any questions? We are pleased to advise you.