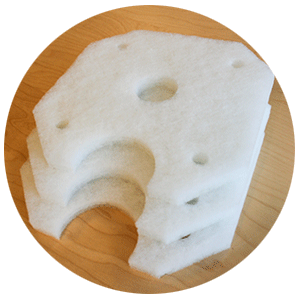
One of the uses of filter fleece is the separation of solids from liquids in wet filtration. Good filter technology is critical to the outcome of both the separation of harmful chemicals as well as juice production in the food industry. In many applications, the material is fabricated to suit specific technical processes, some of which are in continuous operation. The capacity for individual fabrication of filters and large filters, as well as the immediate availability of the materials to the operators, are a strong argument for the use of laser technology.
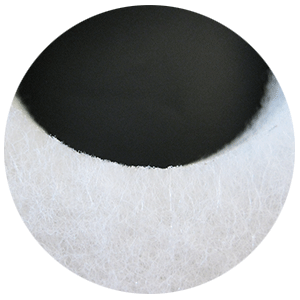
The material is not only used there, but also for pressure belt filters, vacuum filters, round bag filters, bag filters, basket filters and bio-filters.
Cutting of such fabrics with conventional methods, such as punching using a cutter, is complex and involves the application of force. It creates a lot of dust and costs, because the cutting edges often fray, so further material around the cutting edge has to be factored in from the start. The tools are subject to wear and must be replaced which is also costly and time-consuming. In addition, the shapes cannot be freely selected as dieboards are required.
In this situation, the cutting of the fabric with a laser cutting system offers many advantages:
- Automatic welding of the cutting edges prevents fraying
- No tool wear - no reduction in quality
- High flexibility in the daily use of the laser system through numerous additional options
- High precision and repetition accuracy
- Virtually dust-free cutting
- Optimal material utilization
- No application of force through stretching or punching
- Large format cutting, roll width up to 3,200 mm
- Optional automatic material feed and removal
For further information please click the links below:
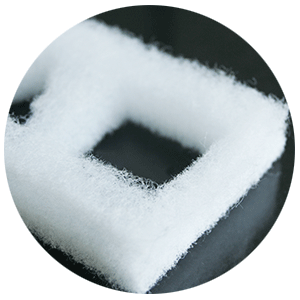
The automatic material feed combined with a removal table increases productivity by more than 50% and guarantees constant cutting quality at the same time.
An example is the use of gravity filters for the purification of liquids. In this type of filtration, the filter fleece is carried on a continuous metal web belt. The liquid runs between the belt and filter fleece. Gravity pulls the liquid through the filter fleece on which the solids settle. The filtrate is collected under the filter and transported further from there.
Do you have any questions? We are pleased to advise you.