Which parameters can I configure?
- Selecting the right cutting nozzle
- Setting the correct distance between nozzle and material
- Setting the process gas
How do these parameters affect the cutting process?
- The material melt is driven from the cutting gap
- Cooling of the heat-affected zone at the focal point
- Prevention of the ignition of cutting emissions
- Protection of the optical lens
What are the effects of optimised settings?
- Neat material surfaces (material-dependent)
- Back of material is free of smoke deposits
- Uniform cut edges
- Smaller cutting widths
- Fewer oxidisation marks

Please observe all warnings and the information in your operating instructions!
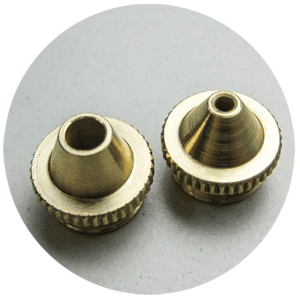
1) Selecting the right cutting nozzle:
You can choose from two different nozzle types, with either a diameter of 2.0 or 4.0 mm. Depending on the nozzle diameter, different effects are achieved.
For replacing the cutting nozzles, please either switch off the laser system or use the tool changeover mode (F4). The cutting nozzles are at the bottom of the laser head and can be easily unscrewed by hand. Please do not use tools for tightening the nozzles, as otherwise the cutting nozzles might be difficult to loosen again.
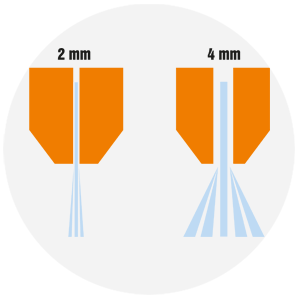
Effects when selecting the cutting nozzle:
With a small nozzle diameter (2.0 mm), a fine jet of compressed air achieves particularly neat cut edges and material surfaces.
A wide jet (4.0 mm) generates a cooling effect on the material surface. A weak, wide air stream is beneficial to engraving applications and makes it possible to have polished cut edges in acrylic glass.
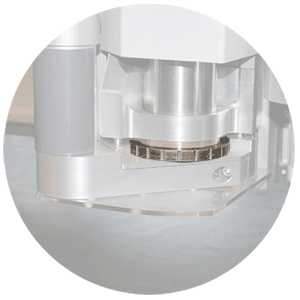
2) Setting the correct distance between nozzle and material:
The free operating distance from the cutting nozzle to the process material is adjusted via the thumb wheel.The nozzle is the deepest point of the laser head. Before adjusting the distance, it must be checked whether the reference value is set to 0 (z=0). If this is not the case, perform an initialisation of the Z-axis on the material support surface as described in your operating instructions.
Now the distance between the nozzle and the material can be fine-tuned.
4 turn clicks = 1 mm separation gap
Minimum distance = 2 mm
Maximum distance = 10 mm
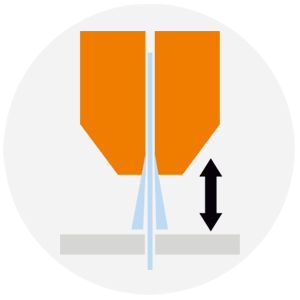
Effects when setting the distance:
The smaller the distance, the more air pressure is applied to the cutting gap. So in general, more cutting emissions are blown out of the gap, so that there is less build-up of smoke. If you increase the distance, the air pressure applied to the cutting gap decreases.
Example: If you increase the distance when cutting acrylic, you create smooth cut edges, but not all flammable gases might be blown into the exhaust channels anymore. So the point needs to be determined at which the optimum ratio between the formation of flames (due to the flammable gases) and smooth cut edges is achieved.
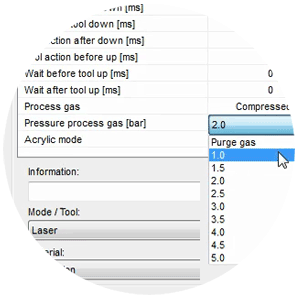
3) Setting the process gas:
The process gas is configured via your operating software.
First of all, select the setting “Process gas” and select the “Compressed air” parameter.
In the second step you can determine the compressed air under “Process gas pressure”. The smallest value is “purge gas”. Otherwise, you can choose between “1 and 5 bar”.
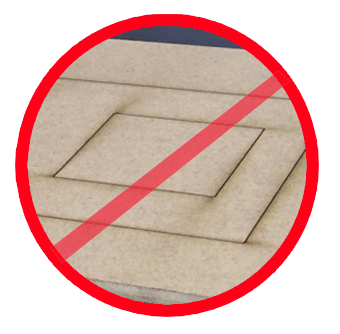
Effects of the process gas setting:
Little pressure might result in the gases being generated during the laser process not being blown out of the cutting gap completely. This can lead to an increased build-up of smoke deposits. For example, little pressure during the cutting of wood can result in darker cut edges.
More pressure has the same effect as little nozzle distance to the material. The gases being generated during the laser process are flushed out of the cutting gap. However, too much pressure can generate a turbulence, which in turn can result in poorer outcomes.
The parameters described above influence each other. The laser power as well as the speed also influence the quality of the cut edge. With the individual configuration of these parameters, you can achieve optimum results for your material.
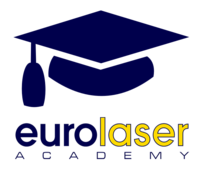
Take advantage of our numerous training options, to optimise your know-how of these and other topics in a targeted way.
Do you have any questions? We are pleased to advise you.